Dalam era industri yang semakin kompetitif, perusahaan-perusahaan dituntut untuk terus berinovasi dan meningkatkan efisiensi. Salah satu pendekatan yang telah terbukti efektif dalam mencapai tujuan tersebut adalah Lean Manufacturing. Konsep ini tidak hanya sekadar metode produksi, tetapi juga filosofi manajemen yang bertujuan untuk menciptakan nilai maksimal bagi pelanggan dengan menghilangkan segala bentuk pemborosan.
Apa Itu Lean Manufacturing?
Lean Manufacturing adalah sistem manajemen produksi yang berfokus pada penghilangan pemborosan (waste) dalam proses produksi. Pemborosan yang dimaksud adalah segala aktivitas yang tidak menambah nilai bagi pelanggan, seperti waktu tunggu, kelebihan produksi, atau cacat produk. Dengan menghilangkan pemborosan ini, perusahaan dapat meningkatkan efisiensi, mengurangi biaya, dan menghasilkan produk berkualitas tinggi.
Konsep ini pertama kali diperkenalkan oleh Toyota melalui sistem produksinya yang dikenal sebagai Toyota Production System (TPS). TPS dirancang untuk memastikan bahwa setiap langkah dalam proses produksi memberikan nilai tambah bagi pelanggan, sambil meminimalkan sumber daya yang terbuang.
Sejarah Lean Manufacturing
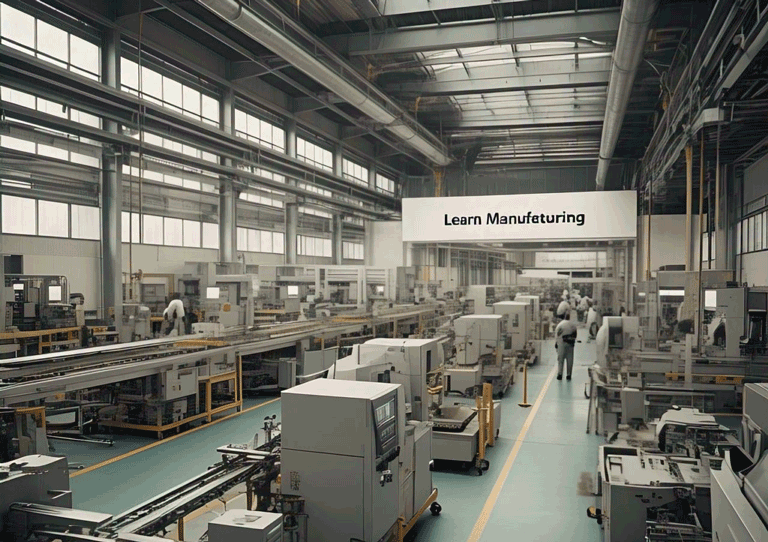
Sejarah Lean Manufacturing tidak dapat dipisahkan dari perkembangan industri otomotif di Jepang pasca Perang Dunia II. Saat itu, Jepang menghadapi keterbatasan sumber daya dan dana, sehingga perusahaan seperti Toyota harus menemukan cara untuk bersaing dengan produsen mobil Amerika yang lebih besar.
Taiichi Ohno, seorang insinyur di Toyota, memainkan peran kunci dalam mengembangkan konsep-konsep Lean. Ia memperkenalkan prinsip-prinsip seperti Just In Time (JIT) dan Kanban, yang bertujuan untuk mengurangi persediaan dan memastikan produksi hanya dilakukan berdasarkan permintaan pelanggan. Selain Ohno, Eiji Toyoda, sepupu pendiri Toyota, juga berkontribusi dalam mengembangkan dan menyebarkan filosofi ini.
Pada tahun 1990-an, konsep Lean Manufacturing mulai diadopsi secara global setelah diterbitkannya buku “The Machine That Changed the World” oleh James P. Womack, Daniel T. Jones, dan Daniel Roos. Buku ini mengungkapkan keunggulan sistem produksi Toyota dan memperkenalkan istilah “Lean” kepada dunia.
5 Prinsip Lean Manufacturing
Lean Manufacturing didasarkan pada lima prinsip utama yang menjadi panduan untuk mencapai efisiensi dan menghilangkan pemborosan. Berikut adalah prinsip-prinsip tersebut:
1. Value (Nilai)
Nilai dalam Lean Manufacturing ditentukan dari perspektif pelanggan. Ini mengacu pada seberapa besar pelanggan bersedia membayar untuk suatu produk atau layanan. Nilai ini tidak hanya mencakup kualitas produk, tetapi juga faktor-faktor seperti kecepatan pengiriman, keandalan, dan kepuasan pelanggan secara keseluruhan.
Produsen atau penyedia layanan bertanggung jawab untuk menciptakan nilai ini dengan cara menghilangkan segala bentuk pemborosan dan biaya yang tidak perlu. Tujuannya adalah mencapai harga yang optimal bagi pelanggan sambil tetap mempertahankan atau meningkatkan keuntungan perusahaan. Dengan fokus pada nilai, perusahaan dapat memastikan bahwa setiap langkah dalam proses produksi benar-benar memberikan manfaat bagi pelanggan.
2. Value Stream (Aliran Nilai)
Aliran nilai merujuk pada seluruh rangkaian aktivitas yang diperlukan untuk mengubah bahan baku menjadi produk jadi atau layanan yang siap diterima pelanggan. Prinsip ini melibatkan analisis mendalam terhadap setiap tahap dalam proses produksi, mulai dari pengadaan bahan mentah hingga distribusi dan pembuangan.
Tujuan dari analisis aliran nilai adalah untuk mengidentifikasi dan menghilangkan aktivitas yang tidak menambah nilai (non-value-adding activities), seperti penundaan, kelebihan produksi, atau penggunaan sumber daya yang tidak efisien. Penyelarasan rantai pasokan juga menjadi kunci dalam mencapai aliran nilai yang optimal, karena hal ini memastikan koordinasi yang baik antara berbagai pihak yang terlibat, seperti pemasok, produsen, dan distributor.
Dalam konteks manufaktur modern, aliran nilai seringkali sangat kompleks dan melibatkan kolaborasi multidisiplin, termasuk insinyur, ilmuwan, perancang, dan tenaga ahli lainnya. Pembuatan produk fisik hanyalah salah satu bagian dari alur kerja yang lebih luas, yang juga mencakup perencanaan, desain, dan pengelolaan logistik.
3. Flow (Aliran)
Menciptakan aliran yang lancar adalah prinsip ketiga dalam Lean Manufacturing. Tujuannya adalah menghilangkan hambatan atau gangguan dalam proses produksi sehingga produk atau layanan dapat mengalir dengan lancar dari satu tahap ke tahap berikutnya.
Proses produksi yang terputus-putus atau tidak terkoordinasi dapat menyebabkan penundaan, penumpukan persediaan, dan biaya tambahan. Dengan menciptakan aliran yang konsisten, perusahaan dapat memastikan bahwa setiap tahap produksi berjalan efisien dan tanpa pemborosan. Hal ini dicapai melalui perbaikan berkelanjutan (continuous improvement) dan penerapan praktik-praktik seperti penyederhanaan proses, standardisasi kerja, dan penggunaan teknologi yang tepat.
Aliran yang baik juga memungkinkan perusahaan untuk merespons permintaan pelanggan dengan lebih cepat dan fleksibel, sehingga meningkatkan kepuasan pelanggan dan daya saing perusahaan.
4. Pull (Tarik)
Prinsip pull mengubah paradigma produksi dari sistem “dorong” (push) menjadi sistem “tarik” (pull). Artinya, produksi hanya dilakukan berdasarkan permintaan aktual pelanggan, bukan berdasarkan prakiraan atau perencanaan yang mungkin tidak akurat.
Dengan menerapkan sistem tarik, perusahaan dapat menghindari kelebihan produksi dan penumpukan persediaan, yang merupakan salah satu bentuk pemborosan terbesar dalam manufaktur. Sistem ini juga memungkinkan perusahaan untuk lebih responsif terhadap perubahan permintaan pasar, sehingga mengurangi risiko kelebihan stok atau kekurangan produk.
Contoh penerapan prinsip pull adalah sistem Just-in-Time (JIT), di mana bahan baku dipesan dan diproduksi hanya ketika dibutuhkan, sehingga meminimalkan biaya penyimpanan dan meningkatkan efisiensi operasional.
Perfection (Kesempurnaan)
Kesempurnaan adalah prinsip terakhir dalam Lean Manufacturing, tetapi ini bukanlah tujuan akhir yang statis. Sebaliknya, kesempurnaan dicapai melalui upaya terus-menerus untuk mengevaluasi dan memperbaiki setiap aspek dari proses produksi.
Prinsip ini menekankan pentingnya budaya perbaikan berkelanjutan (kaizen) di seluruh organisasi. Setiap karyawan, dari level manajemen hingga operator lini produksi, harus terlibat dalam mengidentifikasi masalah, mengusulkan solusi, dan menerapkan perbaikan. Tujuannya adalah untuk mencapai efisiensi maksimal, menghilangkan segala bentuk pemborosan, dan memberikan nilai terbaik kepada pelanggan.
Kesempurnaan juga melibatkan penggunaan alat-alat Lean seperti value stream mapping, 5S, dan root cause analysis untuk terus meningkatkan kualitas dan kinerja operasional. Dengan komitmen yang kuat terhadap prinsip ini, perusahaan dapat terus berkembang dan beradaptasi dengan perubahan pasar.
Strategi Penerapan Lean Manufacturing
Implementasi Lean Manufacturing memerlukan pendekatan yang sistematis dan komitmen dari seluruh organisasi. Berikut adalah beberapa strategi yang dapat digunakan:
1. Pemetaan Aliran Nilai (Value Stream Mapping)
Langkah pertama dalam penerapan Lean Manufacturing ialah pemetaan aliran. Proses ini melibatkan pembuatan peta visual dari seluruh proses produksi, mulai dari pemasok bahan baku hingga pengiriman produk akhir kepada pelanggan. Dengan memetakan aliran nilai, perusahaan dapat mengidentifikasi area yang memerlukan perbaikan dan pemborosan yang harus dihilangkan.
2. 5S (Sort, Set in Order, Shine, Standardize, Sustain)
Metode 5S adalah teknik organisasi tempat kerja yang bertujuan untuk meningkatkan efisiensi dan keselamatan. Ini melibatkan:
- Memisahkan barang-barang yang diperlukan dari yang tidak diperlukan (Sort).
- Menyusun barang-barang dengan cara yang memudahkan akses dan penggunaan (Set in Order).
- Menjaga kebersihan area kerja untuk meningkatkan efisiensi dan mengidentifikasi masalah lebih awal (Shine)
- Mengembangkan standar operasional untuk memastikan konsistensi dan efisiensi (Standardize)
- Mempertahankan dan terus meningkatkan praktek 5S untuk memastikan keberlanjutan (Sustain).
3. Kaizen (Perbaikan Berkelanjutan)
Kaizen merupakan filosofi Jepang yang berarti “perbaikan berkelanjutan.” Dalam konteks Lean Manufacturing, Kaizen melibatkan pencarian dan penerapan perbaikan kecil dan bertahap dalam proses produksi. Ini mendorong karyawan di semua tingkat untuk berkontribusi pada upaya perbaikan.
4. Just-In-Time (JIT)
Prinsip Just-In-Time yang melibatkan produksi dan pengiriman barang hanya saat dibutuhkan, bukan berdasarkan prakiraan. Dengan JIT, perusahaan dapat mengurangi persediaan dan menghindari pemborosan yang terkait dengan penyimpanan dan kelebihan produksi.
5. Kanban (Sistem Tarikan)
Kanban adalah sistem visual yang digunakan untuk mengelola aliran produksi dan persediaan. Ini melibatkan penggunaan kartu atau sinyal untuk menunjukkan kapan bahan atau komponen perlu diproduksi atau dipasok. Kanban membantu menjaga aliran produksi yang stabil dan mencegah kelebihan produksi.
6. Peningkatan Kualitas dengan Poka-Yoke
Metode Poka-Yoke untuk mencegah kesalahan atau cacat dengan mengimplementasikan perangkat atau sistem yang memastikan bahwa kesalahan tidak dapat terjadi. Ini bertujuan untuk mengurangi kebutuhan untuk inspeksi dan perbaikan setelah produksi.
Manfaat Lean Manufacturing
Lean Manufacturing adalah pendekatan manajemen operasional yang bertujuan untuk menciptakan nilai maksimal bagi pelanggan dengan menghilangkan segala bentuk pemborosan. Penerapan prinsip-prinsip Lean Manufacturing tidak hanya berdampak pada efisiensi produksi, tetapi juga memberikan manfaat yang luas bagi perusahaan, karyawan, dan pelanggan. Berikut ini penjelasan tentang manfaat-manfaat tersebut:
1. Peningkatan Efisiensi Operasional
Lean Manufacturing membantu perusahaan meningkatkan efisiensi operasional dengan mengidentifikasi dan menghilangkan aktivitas yang tidak menambah nilai (non-value-adding activities). Pemborosan seperti waktu tunggu, kelebihan produksi, atau proses yang tidak perlu dapat dihilangkan melalui analisis mendalam terhadap aliran nilai (value stream mapping).
Dengan menerapkan prinsip-prinsip Lean, perusahaan dapat menciptakan proses yang lebih ramping (lean) dan terorganisir. Hal ini mengarah pada waktu produksi yang lebih cepat, penggunaan sumber daya yang lebih optimal, dan alur kerja yang lebih lancar. Sebagai contoh, dengan menghilangkan hambatan dalam proses produksi, perusahaan dapat mengurangi waktu siklus (cycle time) dan meningkatkan throughput.
2. Reduksi Biaya Operasional
Salah satu manfaat utama Lean Manufacturing adalah kemampuannya untuk mengurangi biaya operasional. Dengan menghilangkan pemborosan seperti kelebihan produksi, persediaan berlebih, atau waktu tunggu yang tidak perlu, perusahaan dapat menghemat biaya secara signifikan.
Contohnya, sistem Just-in-Time (JIT) yang merupakan bagian dari Lean Manufacturing memastikan bahwa bahan baku hanya dipesan dan diproduksi ketika dibutuhkan. Hal ini mengurangi biaya penyimpanan persediaan dan menghindari risiko keusangan atau kerusakan barang. Selain itu, pengurangan waktu tunggu dan peningkatan efisiensi proses juga berkontribusi pada penghematan biaya tenaga kerja dan energi.
3. Peningkatan Kualitas Produk
Lean Manufacturing menekankan pentingnya perbaikan berkelanjutan (continuous improvement) dan pencegahan cacat sejak dini. Salah satu metode yang sering digunakan adalah Poka-Yoke, yaitu sistem yang dirancang untuk mencegah kesalahan manusia dalam proses produksi.
Dengan fokus pada kualitas, perusahaan dapat mengurangi jumlah produk cacat dan meningkatkan konsistensi kualitas produk. Hal ini tidak hanya menghemat biaya yang terkait dengan perbaikan atau pengembalian produk, tetapi juga meningkatkan kepuasan pelanggan. Pelanggan akan lebih percaya pada merek yang konsisten memberikan produk berkualitas tinggi.
4. Responsivitas terhadap Permintaan Pelanggan
Prinsip pull dalam Lean Manufacturing memungkinkan perusahaan untuk merespons permintaan pelanggan dengan lebih cepat dan akurat. Berbeda dengan sistem produksi tradisional yang mengandalkan prakiraan permintaan, sistem tarik memastikan bahwa produksi hanya dilakukan berdasarkan permintaan aktual.
Hal ini mengurangi risiko kelebihan persediaan (overstocking) atau kekurangan produk (stockouts). Selain itu, dengan mengurangi waktu tunggu dan meningkatkan fleksibilitas produksi, perusahaan dapat memenuhi permintaan pelanggan dengan lebih cepat, sehingga meningkatkan kepuasan pelanggan dan daya saing perusahaan.
5. Peningkatan Kepuasan dan Motivasi Karyawan
Lean Manufacturing tidak hanya berfokus pada proses produksi, tetapi juga melibatkan karyawan dalam upaya perbaikan berkelanjutan. Keterlibatan karyawan dalam mengidentifikasi masalah, mengusulkan solusi, dan menerapkan perbaikan dapat meningkatkan rasa kepemilikan dan kebanggaan terhadap pekerjaan mereka.
Selain itu, penerapan praktik Lean seperti 5S (Sort, Set in Order, Shine, Standardize, Sustain) menciptakan lingkungan kerja yang lebih teratur, bersih, dan aman. Hal ini tidak hanya meningkatkan efisiensi kerja, tetapi juga meningkatkan kepuasan dan motivasi karyawan. Karyawan yang merasa dihargai dan dilibatkan dalam proses pengambilan keputusan cenderung lebih produktif dan berkomitmen terhadap perusahaan.
6. Peningkatan Fleksibilitas dan Inovasi
Dengan mengurangi kompleksitas dan pemborosan dalam proses produksi, Lean Manufacturing memungkinkan perusahaan untuk lebih fleksibel dalam merespons perubahan pasar. Perusahaan dapat dengan cepat menyesuaikan produksi sesuai dengan tren atau permintaan baru, sehingga tetap kompetitif di pasar yang dinamis.
Selain itu, budaya perbaikan berkelanjutan mendorong inovasi di semua level organisasi. Karyawan didorong untuk berpikir kreatif dan mengusulkan ide-ide baru yang dapat meningkatkan efisiensi atau menciptakan nilai tambah bagi pelanggan.
7. Peningkatan Kepuasan Pelanggan
Pada akhirnya, semua manfaat Lean Manufacturing bermuara pada peningkatan kepuasan pelanggan. Dengan mengurangi biaya, meningkatkan kualitas, dan merespons permintaan dengan lebih cepat, perusahaan dapat memberikan produk atau layanan yang lebih baik kepada pelanggan.
Pelanggan akan merasa lebih puas ketika mereka menerima produk berkualitas tinggi, dengan harga yang kompetitif, dan dalam waktu yang lebih singkat. Kepuasan pelanggan yang tinggi tidak hanya meningkatkan loyalitas pelanggan, tetapi juga dapat menjadi sumber referensi positif yang mendatangkan pelanggan baru.
8 Jenis Pemborosan (Waste) dalam Lean Manufacturing
Salah satu inti dari Lean Manufacturing adalah menghilangkan segala bentuk pemborosan (waste) dalam proses produksi. Pemborosan ini tidak hanya merugikan perusahaan dari segi biaya, tetapi juga mengurangi efisiensi, kualitas, dan kepuasan pelanggan. Dalam Lean Manufacturing, terdapat 8 jenis pemborosan yang dikenal dengan istilah “8 Waste”. Mari kita bahas satu per satu secara detail.
1. Overproduction (Produksi Berlebihan)
Overproduction terjadi ketika perusahaan memproduksi barang atau jasa lebih banyak daripada yang dibutuhkan oleh pelanggan atau lebih cepat dari yang diperlukan. Ini adalah salah satu bentuk pemborosan paling merugikan karena menimbulkan efek domino pada jenis waste lainnya
Contoh dalam Praktik:
- Sebuah pabrik memproduksi 1.000 unit produk, padahal permintaan pelanggan hanya 700 unit.
- Memproduksi barang sebelum ada pesanan resmi dari pelanggan.
Dampak Negatif:
- Produk yang tidak terjual memerlukan ruang penyimpanan, yang berarti biaya sewa gudang dan asuransi meningkat.
- Produk yang terlalu lama disimpan bisa menjadi usang atau tidak laku dijual.
- Bahan baku, energi, dan tenaga kerja yang digunakan untuk produksi berlebihan menjadi sia-sia.
Cara Mengatasi:
- Menerapkan sistem Just-In-Time (JIT) untuk memproduksi hanya saat ada permintaan.
- Menggunakan alat Kanban untuk mengontrol aliran produksi berdasarkan kebutuhan aktual.
2. Inventory Excess (Persediaan Berlebihan)
Inventory excess terjadi ketika perusahaan menyimpan bahan baku, barang setengah jadi, atau produk jadi dalam jumlah yang melebihi kebutuhan. Persediaan berlebihan seringkali dianggap sebagai “asuransi” terhadap ketidakpastian permintaan, tetapi sebenarnya justru menimbulkan pemborosan.
Contoh dalam Praktik:
- Menyimpan ribuan komponen elektronik di gudang, padahal hanya sebagian kecil yang digunakan dalam waktu dekat.
- Memiliki stok produk jadi yang menumpuk karena overproduction.
Dampak Negatif:
- Gudang yang penuh memerlukan biaya sewa, listrik, dan pemeliharaan.
- Barang yang disimpan terlalu lama bisa rusak, kadaluarsa, atau menjadi usang.
- Uang yang seharusnya bisa digunakan untuk investasi lain justru terikat dalam persediaan.
Cara Mengatasi:
- Menerapkan sistem Just-In-Time (JIT) untuk mengurangi persediaan.
- Menggunakan Value Stream Mapping untuk mengidentifikasi area yang menyebabkan penumpukan persediaan.
3. Waiting Time (Waktu Tunggu)
Waiting time adalah waktu yang terbuang karena menunggu proses selanjutnya. Ini bisa terjadi karena ketidakseimbangan aliran produksi, keterlambatan pasokan, atau masalah teknis.
Contoh dalam Praktik:
- Karyawan menunggu mesin selesai bekerja sebelum bisa melanjutkan tugas mereka.
- Material tertunda di gudang karena truk pengirim terlambat.
Dampak Negatif:
- Waktu yang terbuang berarti pekerjaan tidak selesai tepat waktu.
- Proses produksi menjadi lebih lama dari yang seharusnya.
- Menunggu terlalu lama bisa menurunkan moral dan motivasi kerja.
Cara Mengatasi:
- Menyeimbangkan aliran produksi dengan Line Balancing.
- Meningkatkan koordinasi antara departemen untuk mengurangi waktu tunggu.
4. Transportation (Transportasi)
Transportation waste terjadi ketika material atau produk dipindahkan lebih sering atau lebih jauh dari yang diperlukan. Ini termasuk perpindahan antar gudang, antar mesin, atau antar departemen.
Contoh dalam Praktik:
- Material dipindahkan dari gudang A ke gudang B hanya untuk diproses di mesin yang sebenarnya bisa ditempatkan di dekat gudang A.
- Pengiriman komponen dari pemasok yang jaraknya terlalu jauh.
Dampak Negatif:
- Semakin jauh jarak, semakin tinggi biaya pengiriman.
- Material yang sering dipindahkan rentan rusak atau hilang.
- Perpindahan yang tidak efisien memperlambat proses produksi.
Cara Mengatasi:
- Merancang ulang tata letak pabrik untuk meminimalkan jarak perpindahan material.
- Menggunakan sistem Kanban untuk mengontrol aliran material.
5. Over-Processing (Proses Berlebihan)
Over-processing terjadi ketika perusahaan melakukan proses produksi yang tidak diperlukan oleh pelanggan atau melebihi standar yang ditetapkan. Ini termasuk penggunaan bahan baku yang terlalu mahal atau langkah-langkah produksi yang berlebihan.
Contoh dalam Praktik:
- Menggunakan cat berkualitas tinggi untuk produk yang sebenarnya tidak memerlukan finishing sempurna.
- Menambahkan fitur pada produk yang tidak diminta oleh pelanggan.
Dampak Negatif:
- Bahan baku dan energi yang digunakan menjadi sia-sia.
- Proses yang berlebihan memerlukan biaya tambahan.
- Proses yang tidak perlu memperpanjang waktu siklus produksi.
Cara Mengatasi:
- Menganalisis kebutuhan pelanggan dengan cermat untuk menghindari proses yang tidak diperlukan.
- Menggunakan Value Stream Mapping untuk mengidentifikasi langkah-langkah yang berlebihan.
6. Motion (Gerakan)
Motion waste terjadi ketika karyawan atau mesin melakukan gerakan yang tidak perlu selama proses produksi. Ini bisa berupa pergerakan fisik karyawan atau pergerakan mesin yang tidak efisien.
Contoh dalam Praktik:
- Karyawan harus berjalan bolak-balik untuk mengambil alat atau material.
- Mesin yang bergerak terlalu sering karena tata letak yang buruk.
Dampak Negatif:
- Gerakan yang tidak perlu membuat karyawan cepat lelah.
- Waktu yang terbuang untuk gerakan tidak produktif.
- Gerakan berulang yang tidak ergonomis bisa menyebabkan cedera.
Cara Mengatasi:
- Merancang ulang tata letak kerja untuk meminimalkan gerakan.
- Menerapkan prinsip 5S untuk mengatur area kerja dengan lebih baik.
7. Defects (Cacat Produk)
Defects adalah produk yang tidak memenuhi standar kualitas atau spesifikasi yang ditetapkan. Cacat produk bisa terjadi karena kesalahan proses, bahan baku yang buruk, atau human error.
Contoh dalam Praktik:
- Produk elektronik yang tidak berfungsi karena kesalahan perakitan.
- Makanan kemasan yang rusak karena proses pengemasan yang salah.
Dampak Negatif:
- Produk cacat harus diperbaiki atau dibuang, yang memerlukan biaya tambahan.
- Pelanggan yang kecewa bisa beralih ke kompetitor.
- Bahan baku dan tenaga kerja yang digunakan untuk produk cacat menjadi sia-sia.
Cara Mengatasi:
- Menerapkan sistem Poka-Yoke untuk mencegah kesalahan produksi.
- Melakukan inspeksi kualitas secara berkala.
8. Underutilized Talent (Keterampilan Karyawan Tidak Termanfaatkan)
Underutilized talent terjadi ketika keterampilan, pengetahuan, atau ide karyawan tidak digunakan secara optimal oleh perusahaan. Ini adalah bentuk pemborosan yang sering diabaikan, padahal karyawan adalah aset berharga.
Contoh dalam Praktik:
- Karyawan dengan keahlian khusus hanya diberikan tugas rutin yang tidak memanfaatkan keahliannya.
- Ide-ide kreatif karyawan tidak didengar atau diabaikan oleh manajemen.
Dampak Negatif:
- Karyawan yang tidak diberdayakan tidak bisa berkontribusi pada perbaikan proses.
- Karyawan merasa tidak dihargai, yang bisa menurunkan motivasi dan produktivitas.
- Karyawan berbakat mungkin memilih untuk pindah ke perusahaan lain.
Cara Mengatasi:
- Menerapkan budaya Kaizen yang melibatkan karyawan dalam proses perbaikan.
- Memberikan pelatihan dan kesempatan pengembangan karir.
Tantangan dalam Menerapkan Lean Manufacturing
Meskipun Lean Manufacturing menawarkan banyak manfaat seperti peningkatan efisiensi, pengurangan limbah, dan peningkatan kualitas, penerapannya tidak selalu berjalan mulus. Berikut adalah beberapa tantangan utama dalam mengadopsi sistem Lean Manufacturing:
1. Perubahan Budaya
Salah satu tantangan terbesar dalam menerapkan Lean Manufacturing adalah perubahan budaya di dalam organisasi. Lean bukan sekadar sekumpulan teknik atau alat produksi, tetapi juga filosofi yang mengharuskan semua karyawan terlibat aktif dalam upaya perbaikan berkelanjutan (Kaizen).
- Banyak karyawan, terutama yang sudah terbiasa dengan cara kerja lama, mungkin merasa tidak nyaman atau bahkan menolak perubahan.
- Lean hanya akan berhasil jika didukung penuh oleh manajemen tingkat atas dan diterapkan secara konsisten.
- Semua level dalam organisasi, dari pekerja lini produksi hingga eksekutif, harus memahami dan menerapkan prinsip Lean agar dapat berjalan efektif.
2. Investasi Awal yang Signifikan
Meskipun Lean Manufacturing bertujuan untuk mengurangi pemborosan dan meningkatkan efisiensi, penerapannya sering kali membutuhkan investasi awal yang cukup besar.
- Karyawan dan manajemen perlu dilatih agar memahami konsep Lean dan cara mengaplikasikannya dengan benar.
- Implementasi Lean mungkin memerlukan perubahan tata letak fasilitas, pembelian peralatan baru, atau penerapan sistem manajemen yang lebih canggih.
- Dalam tahap awal, perusahaan mungkin mengalami peningkatan biaya operasional sebelum manfaat dari Lean benar-benar terasa.
3. Ketidakcocokan untuk Semua Industri
Meskipun Lean Manufacturing banyak diterapkan dalam industri manufaktur, tidak semua jenis produksi atau bisnis cocok dengan prinsip ini.
- Lean lebih efektif dalam lingkungan produksi yang stabil dan berulang. Industri dengan permintaan yang sangat bervariasi atau produk yang sangat custom mungkin kesulitan mengadopsinya.
- Beberapa bisnis memerlukan fleksibilitas lebih dalam proses produksi, yang kadang bertentangan dengan prinsip Lean yang mengutamakan standarisasi dan efisiensi.
- Perusahaan kecil dengan sumber daya terbatas mungkin mengalami kesulitan dalam mengalokasikan dana dan tenaga untuk menerapkan Lean secara optimal.
Walau terdapat beberapa kelemahan, Lean dapat diterapkan di seluruh perusahaan, baik yang bergerak di bidang produk maupun jasa. Penerapan Lean secara menyeluruh disebut Lean Enterprise, di mana Lean Manufacturing menjadi bagian darinya. Implementasi Lean Enterprise memerlukan dukungan teknologi informasi terintegrasi, seperti ERP (Enterprise Resource Planning) atau RFID (Radio Frequency Identification). Jika diterapkan dengan baik, sistem ini dapat meningkatkan keunggulan bersaing dan kinerja perusahaan secara signifikan.
Baca juga:
- Holding Company Adalah dan Contohnya di Indonesia
- Ini Jenis-Jenis Fintech yang Berkembang di Indonesia
- Ini 7 Manfaat Fintech bagi Masyarakat
- Apa Itu Business Development? Tugas, dan Keahliannya
- Apa Itu Disrupsi Digital? Dampak dan Contoh
- Inovasi Produk: Pengertian, Fungsi, Manfaat, dan 10 Contoh
Referensi
- Feld, W. M. (2000). Lean Manufacturing: Tools, Techniques, and How to Use Them. CRC Press.
- Liker, J. K. (2004). The Toyota Way: 14 Management Principles from the World’s Greatest Manufacturer. McGraw-Hill.
- Ohno, T. (1988). Toyota Production System: Beyond Large-Scale Production. Productivity Press.
- Shingo, S. (2018). Fundamental Principles of Lean Manufacturing. Enna Products Corporation.
- Womack, J. P., Jones, D. T., & Roos, D. (1990). The Machine That Changed the World: The Story of Lean Production. Free Press.
- Gupta, S., Jain, S. K., & Kumar, S. (2015). Lean manufacturing: A Review. International Journal of Engineering Research and Applications, 5(6), 29-35.
- Meesena, W., & Thompson, R. (2022). Optimizing Product Wheel Time in Lean Manufacturing Systems. arXiv preprint arXiv:2210.00114.
- Sari, D. R., & Sari, R. M. (2020). Penerapan Lean Manufacturing di Sebuah Perusahaan Keramik. Jurnal Teknologi Industri, 9(2), 123-130.
- Siregar, M. R., & Siregar, R. (2019). Penerapan Lean Manufacturing Untuk Meminimalkan Waste pada Proses Produksi. Seminar Nasional Penelitian dan Pengabdian pada Masyarakat, 2(1), 45-52.
- Marulanda-Grisales, N., & Gaitán, S. (2017). Penerapan Lean Manufacturing di Industri Makanan dan Minuman. IKRAITH-EKONOMIKA, 1(3), 1-10.